Paul E. Sumner1
Dewey Lee2
Aflatoxin is a naturally occurring toxin produced by the fungus Aspergillus flavus. The fungus can be recognized by a gray-green or yellow-green mold growing on corn kernels in the field or in storage (Figure 1). Plant stress due to drought, heat or insect damage during fungus growth usually increases aflatoxin levels. Aflatoxin contamination will reduce feeding value and hinder sales. Because it is extremely poisonous to warm-blooded animals even at relatively low levels, grain handling facilities often check for the presence of the toxin before purchasing corn.
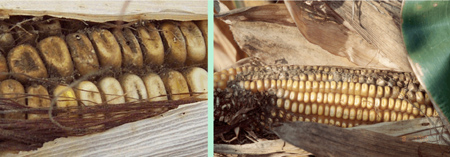
Figure 1. Aspergillus rot symptoms in corn ear and kernels.
Aspergillus flavus is a common fungus found in soil and debris. Since it occurs so frequently in nature, particularly as airborne spores, it can be found on most grain in the field and in storage. Moisture and heat stress is commonly associated with most aflatoxin outbreaks. This problem generally occurs every year in Georgia, since the state's weather during grain development is ideal for growth of the fungus. Sound agronomic practices and post-harvest practices must be followed to reduce or prevent contamination or buildup once the crop is harvested and stored.
Table 1 shows the optimum conditions for Aspergillus growth and aflatoxin development. When temperatures are below 65 degrees F and the moisture of the corn is below 12 to 13 percent, development of the fungus usually stops.
Table 1. Conditions Favoring Aspergillus flavus Development |
Factor |
Optimum |
Range |
Temperature |
86°F |
80-110°F |
Relative Humidity |
85% |
62-99% |
Kernel Moisture |
18% |
13-20% |
Suppression of Potential Aflatoxin Prior to Harvest
Aflatoxin contamination problems are minimized with management such as thoroughly cleaning grain, proper combine adjustment to reduce kernel damage, matching drying capacity to wet corn holding capacity, proper drying, removal of fines and broken kernels, proper grain cooling after drying, and sound storage practices.
Sanitation of equipment is the first step in preventing post-harvest aflatoxin contamination. Clean out all harvesting, handling and drying equipment and storage bins prior to harvest. Remove all broken corn, dust and foreign material that can provide a source of contamination. Check and repair storage bins to prevent moisture leaks from faulty joints or other problems. Clean bins and remove debris to reduce contamination. Use an approved insecticide to treat the bin before filling. Mow around storage bins to discourage insect/rodent activity.
Always remember to provide adequate dust protection for those who work around grain-handling equipment.
Harvest Tips to Reduce Aflatoxin
Research shows most Aspergillus infection occurs on corn in broken and damaged kernels and in foreign material. Damage to the grain seed coat permits easy entrance of molds and fungi, and promotes rapid development of storage rots at high moisture and temperature levels. Heat and drought stress can cause seed coat fractures and increase the opportunity for infection to occur. Aflatoxin can develop within 24 hours in mold- and fungi-infected corn stored under these conditions, even though corn was previously free of aflatoxin.
Harvesting must be done in such a way to prevent damage to the seed coat and to assure maximum cleaning of grain, since damaged seed and foreign material contribute to the development of aflatoxin. The following practices will reduce the likelihood of this problem.
When corn reaches maturity, harvest immediately and dry mechanically. Harvest should begin when the moisture level reaches 28 to 30 percent. Studies have shown that most corn hybrids will normally lose about 0.5 to 0.6 percent moisture per day during the dry-down period. You can reduce field exposure by at least 1 to 2½ weeks by harvesting above 22 percent moisture compared to letting corn dry in the field to 15 percent or less. This will require immediate drying, however.
Irrigated corn generally has fewer problems with Aspergillus infection due to better growing conditions (less drought and heat stress, etc.). If corn is irrigated, harvest the crop outside the pivot separately and store it separately to reduce chances of contaminating good corn. Be sure the clean the combine before harvesting the irrigated corn.
Set combines to minimize grain damage. Set fans higher to clean out light-weight cracked grain and undeveloped kernels. Slowing header seed reduces kernel damage. Ears in contact with the ground for some time usually exhibit higher than normal aflatoxin levels and should not be picked up, if possible.
Combine cylinder/rotor speed should be slow enough and concave clearance as great as possible to provide adequate threshing. Less damage to seed coat occurs with these settings. Install filler plates between cylinder bars to reduce physical damage.
Grain Handling
Do not hold high moisture grain in wagons or trucks longer than 6 hours. Place high moisture corn being held for drying in a holding bin using forced air to keep it as cool as possible.
Use sound sanitation practices in handling grain. Clean augur wells and pits, and clean around dump stations before and after each use. Minimize physical damage by conveyors or from dropping the grain into tall bins.
Dry Properly
Drying temperature and drying time may have an effect on the development of aflatoxin in stored grain. Slow drying with low heat over long periods could promote aflatoxin development.
Layer-in-Bin Drying
Drying corn in deep layers can produce conditions highly favorable for mold development. The drying temperature for this method is increased only 10 to 20 degrees F above outside conditions. The relative humidity in the top layer of grain remains very high for an extended period of time. These factors are favorable for aflatoxin production.
Batch-in-Bin Drying
A lot of grain is batch dried in bins. Wet grain is usually placed about 3 to 4 feet deep in a drying bin and hot air (about 140 degrees F) is forced through the grain, drying the batch normally in less than 24 hours. The grain is then cooled for storage in the same bin or moved to a storage bin and cooled by aeration fans.
This method can be used when storage is available to unload the dryer before putting additional wet grain into the dryer. If the heater is adequate to raise air temperature sufficiently, this method can increase drying rate by a factor of 3 over the layer-in-bin drying method. Chances of aflatoxin being produced with this system are decreased since higher temperature and faster drying are used. To prevent further fungi and mold growth in storage, dry to an average moisture content of 12 percent.
Column Dryers
Aflatoxin production in column dryers operated at high temperatures (180-200 degrees F) and short drying time (1-2 hours) is very unlikely. This is true for batch or continuous flow column type dryers.
Maintain Proper Storage Conditions
Keep moisture in stored grain below 12-13 percent to stop the development of aflatoxin. Also keep insect activity to a minimum.
Cooling the grain below 60 degrees F with outside air as soon as temperatures permit is beneficial in arresting the development of insect populations.
Scalping grain before storage will help remove trash, cracks and shriveled kernels, which are usually high in aflatoxin content. Consider using a grain cleaner at the bin to remove trash before placing the grain into storage.
Storage
Aerate grain in storage when it is at least 10 degrees F warmer than outside air temperature and humidity is below 65 percent. An air flow rate of 1/10 cubic feet per bushel per minute is adequate for cooling grain.
Drying fans can be used to cool grain in a few hours when outside air conditions are favorable. Air should be pulled from the top of the bin and exhausted through the bottom to prevent moisture condensation at the top of the grain during aeration. Never add heat during aeration. Operation of aeration fans during summer is not recommended unless hot spots or a musty odor develop. If this occurs, operate the fan during the coolest part of the day for about 10 minutes until the problem disappears or until the grain can be marketed.
Grain held in storage should be inspected and probed every 3 to 4 weeks. Check for insect activity, high temperatures, mold growth or sprouting at the top of the grain.
Cleaning Corn to Reduce Aflatoxin
Mold, fungi and aflatoxin levels in corn are normally higher in the fine material -- commonly referred to as "fines." Removal of the fines can reduce aflatoxin levels up to 50 percent. Corn having little fine material, however, may not be improved substantially by cleaning.
Sampling Corn
Take extra care to collect representative samples when testing for aflatoxin due to the extreme varia-bility within lots, fields and bins of corn containing aflatoxin. Variability within fields can be attributed to different levels and kinds of stress incurred by the corn crop in different portions of the field.
Substantial variability will also occur in corn sampling because few kernels are normally contaminated. The concentration of these kernels is quite high, however. Increasing the frequency and size of samples gives a clearer indication of the true nature of the crop.
Testing should be done with accurate and reliable methods such as quick test ELISA (enzyme-linked immunity stimulated assays) and gas chromatography, which determines the presence or absence of aflatoxin at levels of 10 ppb or more. Black light screening only tests for the presence of Aspergillus and should not be used to determine the presence of aflatoxin.
Detection methods range from visual observations to chemical analysis. A black light test uses ultra-violet light to illuminate a bright yellow-green fluorescence of a fungal product associated with the toxin. It is used only as a preliminary test, and is most often used by an elevator for initial testing. If the grain sample fluoresces, then further analysis is usually conducted. Chemical analysis is necessary to determine the actual concentration of a toxin. Equipment and kits are available for purchase from several suppliers that are accurate in determining concentrations.
The recommended procedure is to sample periodically from a moving stream, combining these samples to obtain a composite sample of at least 10 pounds of corn. An alternative is to sample with a probe through a storage unit (five perimeter samples and one center sample for each 6 feet of bin height).
In the field, sample individual fields or parts of fields separately. Fields that very in cropping history, tillage practices, irrigation, planting date, soil type or hybrid can differ greatly in aflatoxin vulnerability. Sample a minimum of 10 to 30 locations within each field. Dry samples to 12-14 percent moisture to prevent aflatoxin development during transit or storage. High-moisture samples should be frozen and delivered to the laboratory in the frozen state. Dried samples maintain their quality best if shipped in cloth or paper containers rather than plastic or air-tight containers.
In Georgia, the Georgia Department of Agriculture Seed and Grain Laboratory will test farmer samples free. Mail properly packaged samples to:
Georgia Department of Agriculture
Grain Lab
Highway 41 S
Tifton, GA 31794
229-386-3147
Be sure to include your name and address for the report.
Grain Preservatives
Several organic acids are registered for use on high moisture corn. Most grain can find a safe and legitimate use, however. Cleaning grain by screening or a gravity table can reduce aflatoxin concentrations by removing the most heavily contaminated particles. This can be expensive, however, and it is not possible to predict just how much the aflatoxins will be reduced. Do not use the fine material produced from the cleaning process as feed.
Feeding Contaminated Grain
Aflatoxin-contaminated grain may be used locally for animal feed under the guidelines shown in Table 2. Livestock producers may be willing to buy contaminated corn if it is below 200-300 ppb. You will have to discount the price received, but other options may not be available. Be sure you have an accurate estimate of the aflatoxin level so informed decisions can be made about feeding.
Table 2. FDA Guidelines for Acceptable Aflatoxin Level in Corn Based on Intended Use. (Munkvold, et.al., 2002) |
Intended Use |
Aflatoxin Level (ppb) |
Milk |
none detected |
Corn of unknown destination |
<20 |
Corn for young animals |
<20 |
Corn for dairy cattle |
<20 |
Corn for breeding meat cattle, swine and mature poultry |
<100 |
Corn for finishing swine |
<200 |
Corn for finishing cattle |
<300 |
Binding agents such as sodium bentonite and aluminosilicates have reduced the effects of aflatoxins on livestock. Not all of these materials, however, are the same. Some bentonite clays bind toxins in chemical tests but can release the toxin in the rumen/digestive tract of animals. These products are approved for use in feed although the FDA does not recognize their aflatoxin management properties.
Blending aflatoxin-contaminated grain with clean grain is not legal except in advance of direct feeding operations. Blended grain may not be sold in general commerce. Once aflatoxin levels are known or suspected, it is the owner's responsibility to isolate that corn from general commerce.
Ethanol/Wet Milling
Corn with aflatoxins can be used for ethanol production. Aflatoxins do not accumulate in the ethanol but will be concentrated in the distiller's grains co-product. In wet-mill processing, aflatoxins concentrate in the gluten co-products. A rough estimate is that aflatoxin levels in feed co-products will be 4 times those in while corn.
Ammoniation
Anhydrous ammonia has been shown to react with aflatoxins and reduce their concentrations. This is practice is not approved for interstate commerce, however, so ammoniated grain can only be used on-farm. Ammonia can be applied as a gas or liquid, but either way is a difficult and dangerous procedure and should be done only by an experienced operator.
References
Vincelli, P., G. Parker, and S. McNeill. 1995. Aflatoxins in Corn (Publication No. ID59). University of Kentucky College of Agriculture. p. 7.
Murphy, M. 1998. Laboratory Analysis of Mycotoxins. Proceedings of Minnesota Dairy Health Conference. University of Minnesota Extension, pp. 161-175.
Munkvold, G., et. al. 2002. Aflatoxins in Corn. Iowa State University, University Extension. PM 1800, p. 4.
Status and Revision History
Published on Jul 17, 2003
Published on Feb 20, 2009
Published on May 11, 2009
Published with Full Review on Nov 14, 2012
Published with Full Review on Apr 19, 2017
Published with Minor Revisions on Jun 11, 2024